The state-of-the-art compounding technology of COMPEO meets the extremely high requirements of the polymer industry: a wide range of applications, a large operating window, high flexibility and robustness, as well as consistent process stability, but also operational and operator safety, energy efficiency and reduced operating costs. The result is a system that can be configured from standardized modules for applications well beyond the market segments served before, such as PVC, cable compounds and thermosets. This opens up compounding possibilities for a broad spectrum including engineering plastics with process temperatures up to 400° C.
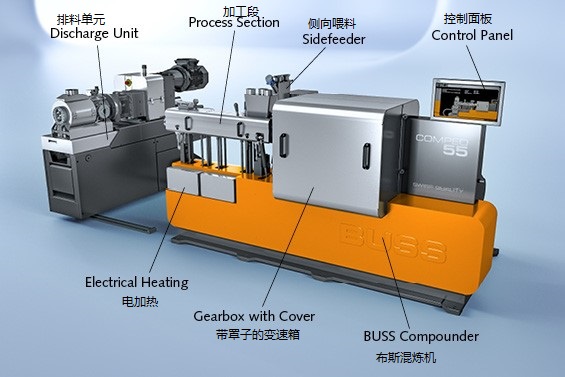
A highly innovative machine concept
There is a basic version with two intake zones. Polymers, additives and some of the fillers are fed through the first inlet opening into the process section. In the melting zone, the polymers are molton and mixed with the additives. In the second feed zone, further fillers are added and distributed homogeneously into the downstream zone. Volatiles and air are removed in the degassing zone before transfer to the discharge unit. For customer-specific and tailor-made solutions, the processing length, type and number of feeders, temperature, degassing and process geometries are defined according to the compounding application.
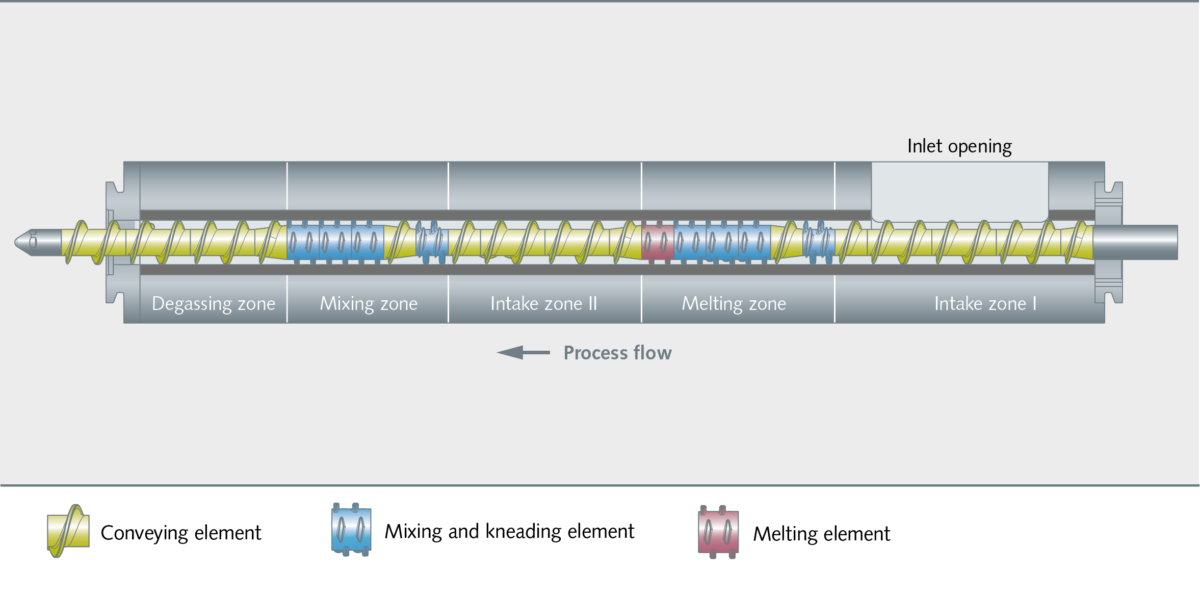
During development the new compounding system, great importance was attached to ergonomics, ease of maintenance, and energy efficiency. Lines and cables are laid as far as possible inside the machine behind easy-to-clean panels. The gearbox is covered with a soundproofing hood that also improves operational safety. To minimize energy losses, the kneader barrel is thermally insulated. Maintenance outlay is minimized by using highly resistant surface-hardened materials in the process zone.
Further development in the process zone
The freely configurable COMPEO process zone opens up new process engineering possibilities through the availability of mixing and kneading elements with two to six rows of screw flights. By combining existing screw technology (three- or four-flights) with newly developed elements, previously conflicting goals – high specific throughput with controllable energy input – can now be achieved at the same time. The COMPEO screw geometries ensure high throughput with up to 20% lower speed. Increasing the volume-related torque by 15% enables the configuration of longer mixing zones. That results in more stable process conditions without a higher energy input. In addition, the process window is significantly larger. Throughput can be varied in a ratio of 1:6, increasing both system flexibility and user-friendliness. It is particularly advantageous for starting up, for small lots, and for inline-processes, where the downstream unit requires consistent product quality even with greatly varying throughput rates.
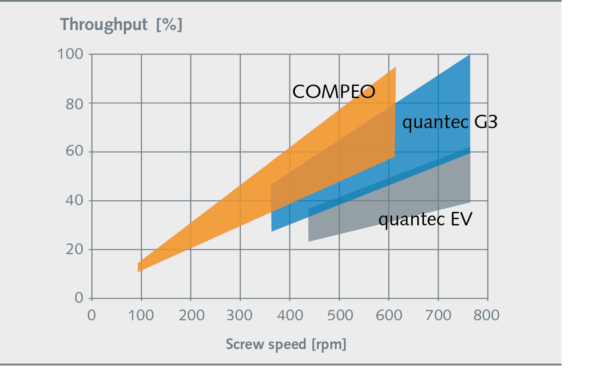
The COMPEO process window with a throughput ratio of 1:6, here using PVC as an example, is considerably larger than those of previous Kneader series machines.
The new state-of-the-art compounder COMPEO is perfect for cable compounds, PVC pelletizing, masterbatch, calendaring, rubber compounds, performance compounds, engineering plastics, thermoplastic elastomers, thermosets, PBT, PET, bitumen, bioplastics, hot melt, friction coatings…