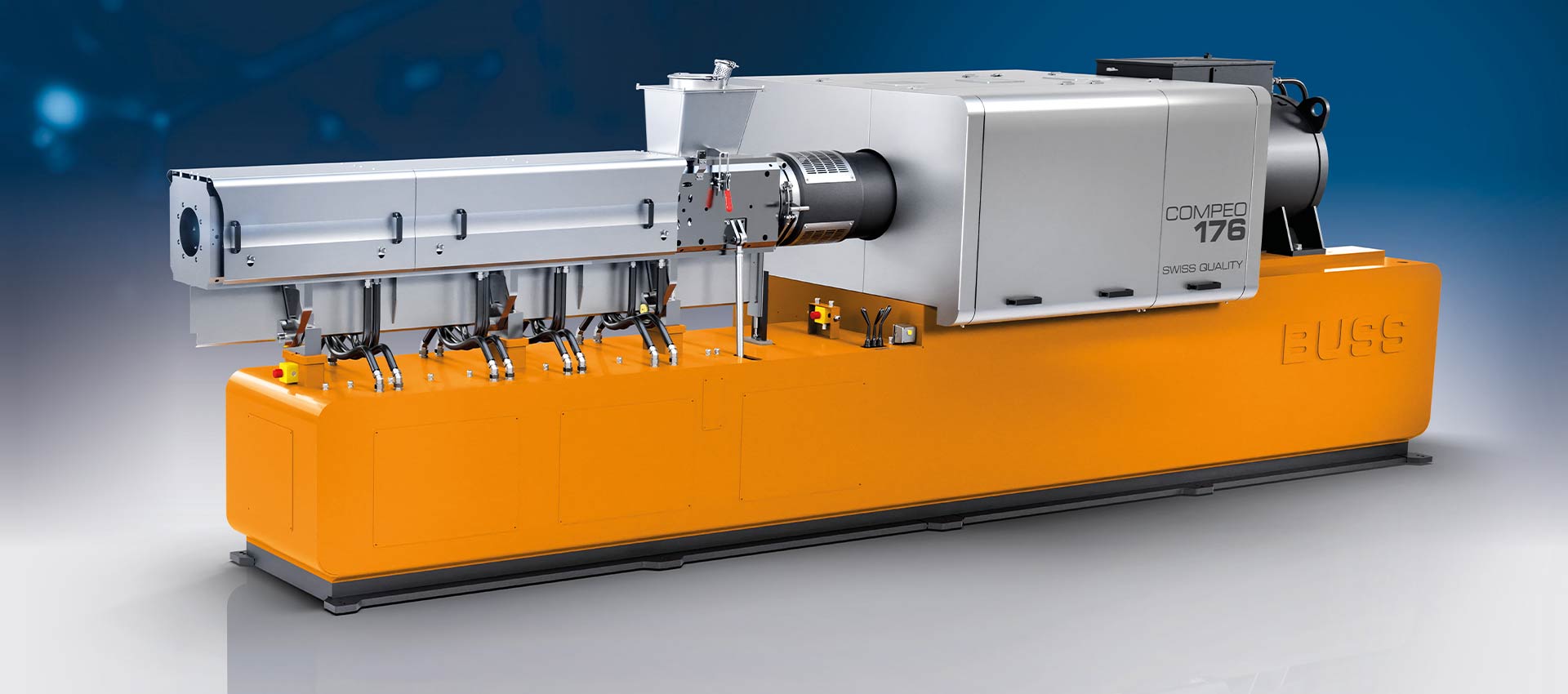
How to process
Battery Electrodes
with COMPEO compounder series.
The importance of Battery Electrode Compounds.
Battery electrode compounds play a critical role in the performance of lithium-ion batteries, which power our portable electronics and are increasingly being used in electric vehicles. These compounds are the key materials in the battery’s anode and cathode, where electrochemical reactions take place during charging and discharging.
Lithium-Ion Battery Electrodes
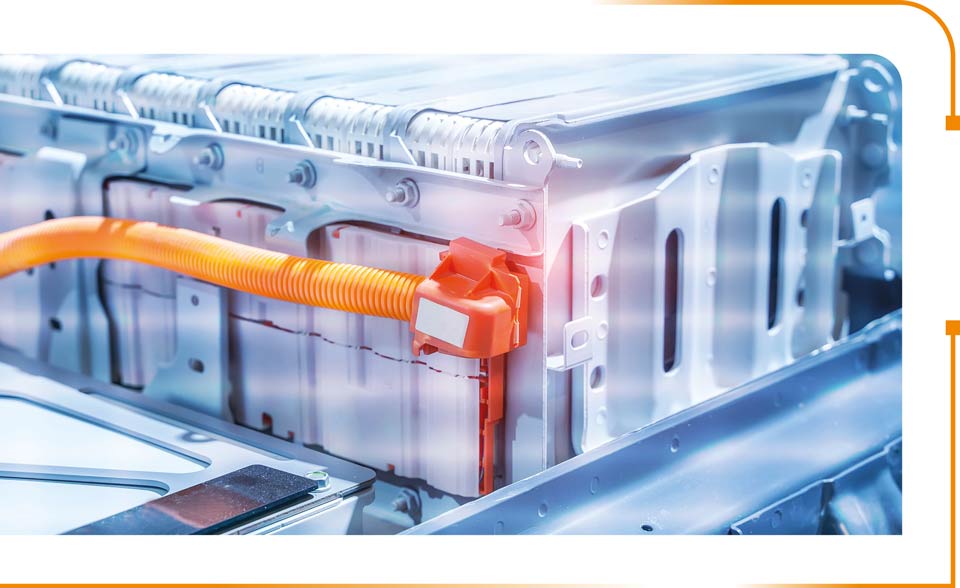
Lithium-ion battery anodes are typically made from graphite, while cathodes are most commonly composed of Lithium Nickel Manganese Cobalt Oxide (NMC). However, other materials, such as silicon or lithium iron phosphate, can also be used. In addition to the active materials, electrode production also involves binders, conductive materials like carbon black or carbon nanotubes (CNTs), and solvents. These additional components help create a homogenous electrode layer that is essential for optimal battery performance.
Challenges in Electrode Manufacturing
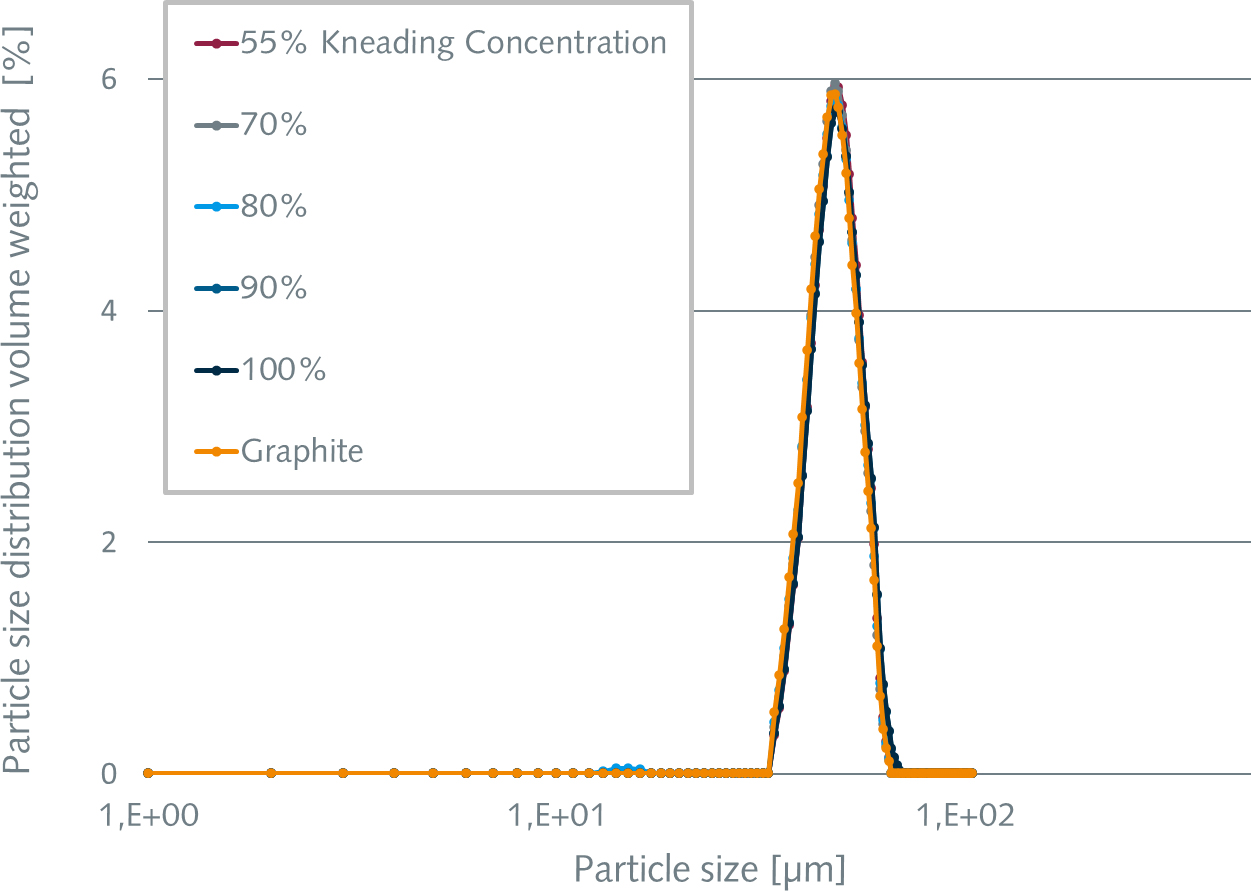
Particle size distribution using varying kneading concentrations
A well-mixed electrode layer is crucial for efficient battery operation. Inconsistent mixing can lead to performance issues and reduced battery life. There are two main types of mixing systems currently used for electrode materials: batch and continuous. While batch mixers can achieve a high degree of homogeneity, they are susceptible to variations between batches. On the other hand, continuous systems may use high shear forces that can damage larger particles in the electrode compound.
Buss Kneaders and Improved Mixing
Buss kneaders offer a solution to the challenges of traditional mixing methods. They are continuous processes that use adjustable shear forces to create a more controlled mixing environment. This helps to preserve the integrity of the particles in the electrode compound, even in low-solvent or dry mixtures, which are becoming increasingly important for next-generation batteries.
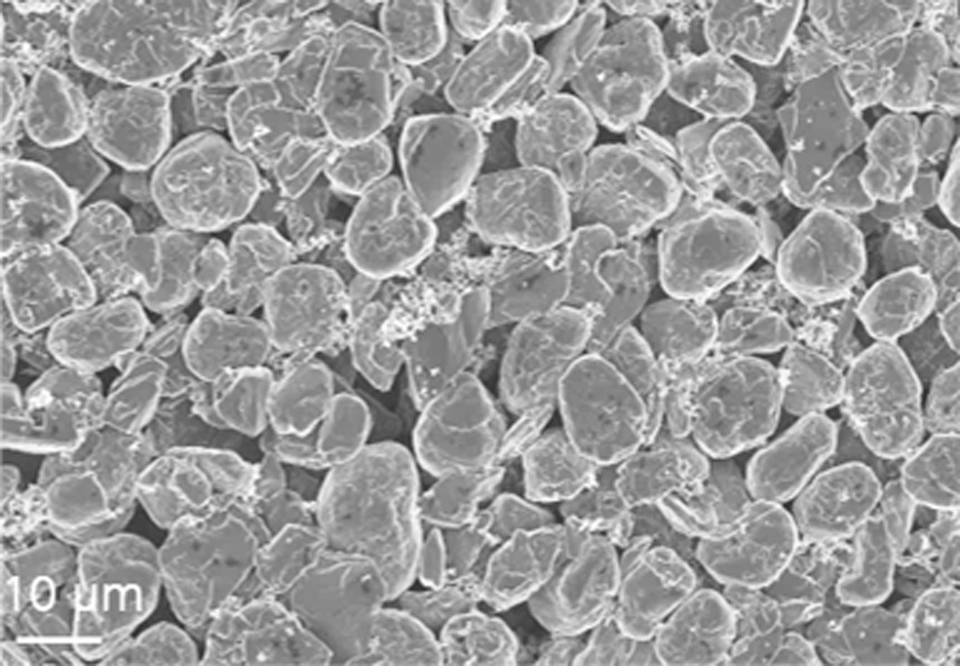
54.5% KC (liquid)
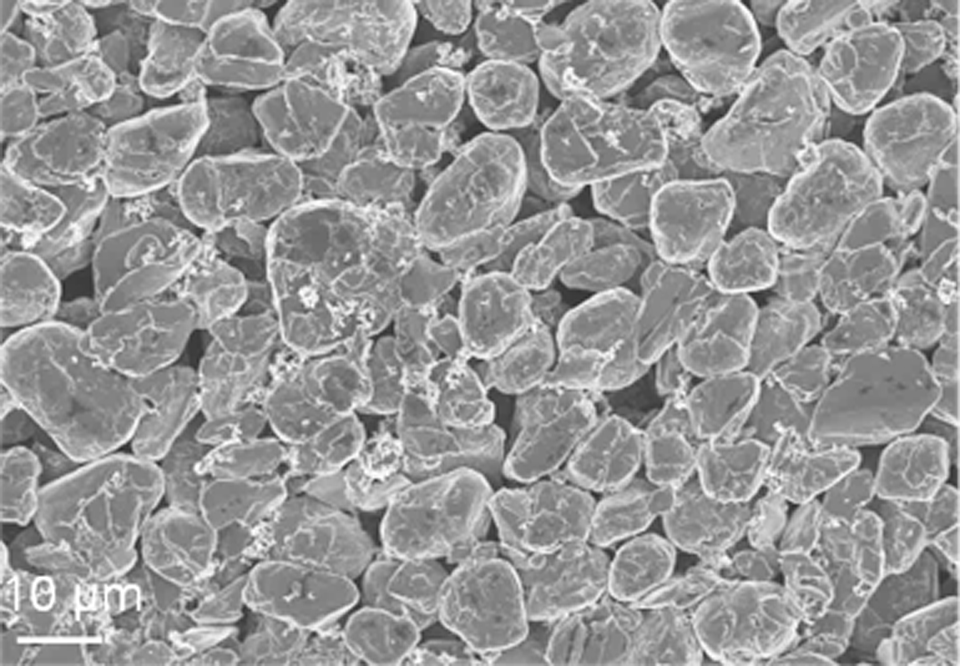
100% KC (dry)
Scanning electron microscopy (SEM) pictures of graphite particles in anode mixtures, liquid (54.5%) and dry (100%) kneading concentration (KC).
The Future of Battery Technology
The trend in lithium-ion battery development is towards low-solvent or dry electrode processes. This can improve safety, reduce environmental impact, and lower production costs. Buss kneaders are well-suited for these dry processes, and Buss also has experience working with similar materials in other applications.
BUSS
– A Partner in Battery Development
COMPEO compounder series.
Buss offers a variety of services to companies developing battery electrode materials. They have a test center with experience in processing both anode and cathode materials, and they collaborate with research centers and plant manufacturers to stay up to date on the latest technologies. Buss is also actively involved in raising awareness about the limitations of traditional mixing systems for battery electrodes and is looking to collaborate with partners to develop new solutions for the future of battery technology.
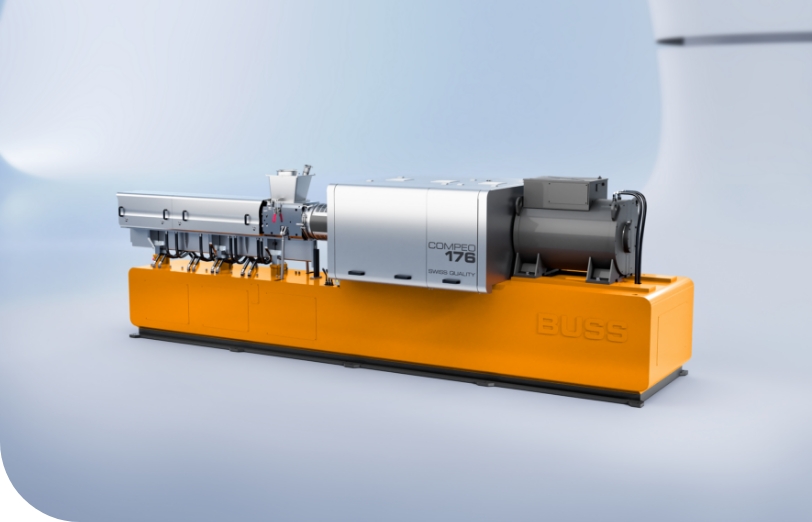