Peroxide Crosslinkable Cable Compounding
Polyethylenes (PE) have outstandingly good insulation properties. A temporary temperature rise, e.g. due to peak loading, can however cause a complete breakdown of PE cable insulation. The relatively low softening or melting point leads to thermo-mechanical failure or even dripping of the Insulation. Cross-linked polyethylene (PEX) is more thermosetting than thermoplastic. It can therefore be used at significantly higher operating temperatures, is mechanically stronger, more resistant to organic liquids, and often enables thinner wall thicknesses. Various cross-linking methods are used.
Typical applications of peroxide crosslinkable cable compounds
Peroxide cross-linkable cable compounds, are also known as PEX-a, have been used for the cable industry ever since the process was patented in the 1960s. The base polymers, peroxide and additives are first mixed intensively at temperatures maintained below 130°C. The cross-linking process takes place directly afterwards on a pressurized high-temperature CV (Continuous Vulcanisation) line. Due to its relative complexity, this technology is used above all for heavy-duty cables. Thanks to the development of water tree resistant formulations and processes, peroxide cross-linkable XLPE is increasingly used for medium voltage (MV) and high voltage (HV) AC cable insulation and for HV DC cables they are the preferred insulation material. Underground power cables for urban supplies are increasingly replacing overhead lines. The same insulation material is very often used for cables connecting offshore wind farms to the grid, and for undersea cables in general. These are global megatrend markets, with high volume and high growth rates accordingly. And for producing the basis of this kind of cable insulation the peroxide crosslinkable cable compounding systems by BUSS are a good partner.
Compounding requirements for peroxide crosslinkable cable compounding
The formulation components for these applications have to be intensively mixed at strictly controlled temperatures, with high plant and product purity. For MV applications the liquid peroxide is directly injected into the melt pool and intensively mixed at low temperatures. The compound is then melt filtered and pelletized. For HV applications, the compounding line is designed and operated to ensure the highest purity. The base polymers are prefiltered and contamination sources are eliminated both internally and externally, so that production takes place under cleanroom conditions.
The success factors of the BUSS Kneader within the whole compounding system in this connection are as follows. Peroxide is directly injected into the process zone and optimally distributed by intensive mixing immediately afterwards. Uniformly moderate shear rates make sure that this occurs at low process temperatures with the least possible polymer breakdown. The cascaded line arrangement of the BUSS Kneader and discharge extruder, furthermore enables product-considerate melt filtering and pelletizing as well as optimal and efficient equipment start-up and operation.
As a reference for this industry, all the compounding lines successfully realized so far exemplify the perfect fusion of BUSS expertise in process technology, plant engineering and design.
Typical plant setup for peroxide crosslinkable cable compounding
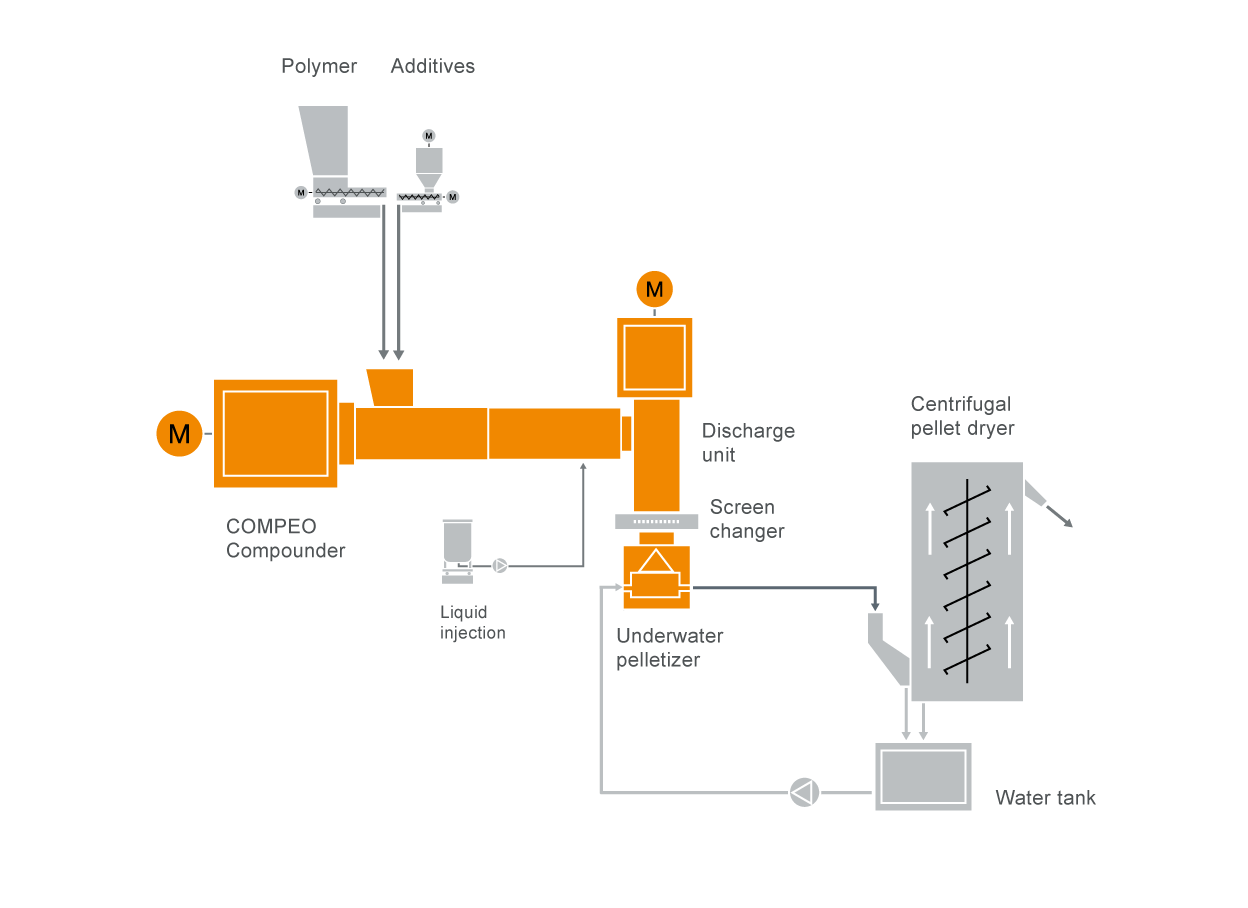
BUSS peroxide crosslinkable cable compounding systems offer the following specific benefits
Learn More
Downloads
-
COMPEO