Semi Conductive Cable Compounding
Semi conductive compounds for cable applications
Medium-voltage (MV) and high-voltage (HV) cable insulation is enclosed between two concentric semi conducting layers to homogenize the electrical field in the insulation material. These layers generally comprise ethylene-based polymers like EVA, EBA or similar, with a high content of conductive materials such as carbon black, graphite, or carbon nanotubes to effect semiconductivity.
Not enough attention was paid at first to how these semi conductive layers affect the insulation material. It was soon discovered, however, that ions in the semiconductors can infiltrate the insulation between the layers and lead to the formation of water trees.
By suitably adjusting the chemical composition of the polymers and respective additives, the outer semi conducting layer can easily be removed from the insulation. This can be useful for cable installation in some cases, and is still required by the regulations in France and the USA. Other countries are increasingly dispensing with the requirement for an easily removable semi conducting layer, whether for cost reasons or because excellent peeling tools are now available. For EPR based compounds, an easily removable semi conducting layer is still required because mechanical removal is difficult. Volumes are rising in pace with the development and growth of polymer MV/HV cable insulations.
Compounding requirements for semi conductive cable compounding
The process requirements for semiconducting cable compounds are very demanding. Conductivity values must be dependable both at room temperatures and at higher operating temperatures. Highly structured carbon black must remain unchanged and be distributed extremely homogeneously to form the required conductive network. The polymers used must be degraded as little as possible. The surfaces of the coextruded layers must be very smooth and uniform. Usually peroxide-based cross-linking is required.
The BUSS Kneader within the semi conductive cable compounding systems meet these complex requirements thanks to its specific strengths: The high content of conductive additives can be introduced at several feed points along the processing section. Immediate mixing at moderate shear rates, with intermediate relaxation phases, ensures excellent distribution without damaging the internal structure of the polymers and conductive materials. The system design flexibility also enables specific attention to the increased viscosity in the process zones through targeted configurations. This allows custom-tailored monitoring and control of the process conditions.
Since the Buss Kneader’s two-stage system separates compounding and pressure build-up, processing is optimized for best possible product quality and throughput, independently of pressurization, melt filtration and pelletizing.
The modular design of the entire BUSS Kneader line makes it easily adaptable. Together with the widely based BUSS processing expertise, the BUSS Kneader has always been a good choice for almost all needs of semi conductive cable compounding in many parts of the world and for many output rate requirements.
Typical plant layout for semi conductive cable compounding systems
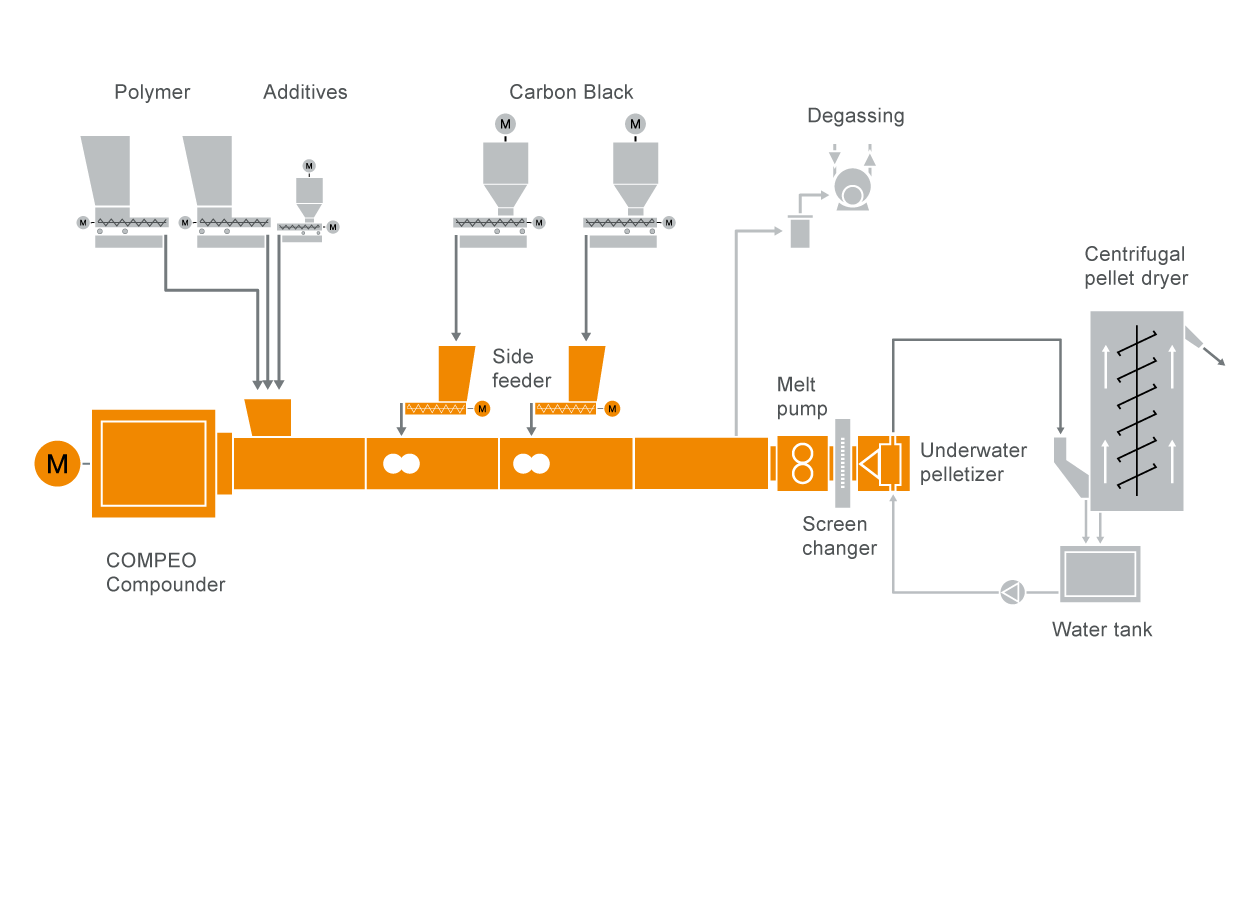
BUSS semi conductive compounding systems offer the following specific benefits
Learn More
Downloads
-
COMPEO