Filled and Reinforced Thermoplastics (FRTP)
There are basically two reasons for working fillers into a plastic matrix: to optimize the compound material properties, such as for breathable foils or sound-absorbing pipes, or to save costs.
Three variables play key roles in the interaction between fillers and polymer matrix:
- Particle shape: a small aspect ratio such as of glass beads, CaCO3 or BaSO4 usually improves the modulus of elasticity, while particles with a large aspect ratio, such as talcum or wollastonite, tend to improve tensile and tear strength as well as the modulus of elasticity.
- Particle size distribution affects how well the fillers are worked in. Important here are the Van-der-Waals cohesion forces between particles more than 1 μm in size, and the dispersive shear forces exerted by the BUSS Kneader within the FRTP compounding system on particles less than 10 μm diameter.
- Surface area of the fillers: the number of potential cohesion points between fillers and polymer chains depends on the specific surface area (m²/g) of the fillers. The larger the fillers surface area, the more cohesion points and the stronger the material (rigidity, tensile strength, tear and impact strength). The surface gloss is also better.
Surface coatings are another important aspect. They can for example influence agglomerate formation, material flowability for easier handling, and adequate wetting during compounding.
Compounding requirements for reinforced compounds
BUSS process expertise is key for highly filled compounds. Apart from optimal distribution of the material flows, particular attention must also be paid to air and moisture entrained during the feeding of fillers. The process geometry must therefore be optimally configured accordingly. With the right configuration, the BUSS Kneader’s large capacities and associated torques enable efficient production of reinforced compounds.
With its outstanding allrounder qualities and enormously wide operating window, the BUSS Kneader can handle the widest range of processes with fillers such as talcum, titanium dioxide or barium sulphate, as well as aluminium (aluminum) or magnesium hydroxides. A welcome side effect of the BUSS Kneader’s moderate shear rate is much less wear and tear than with other screw kneaders. The modular design and resultant adaptability of the entire BUSS Kneader line makes it an excellent choice for compounding filled and reinforced thermoplastics.
Typical plant layout for FRTP compounding systems
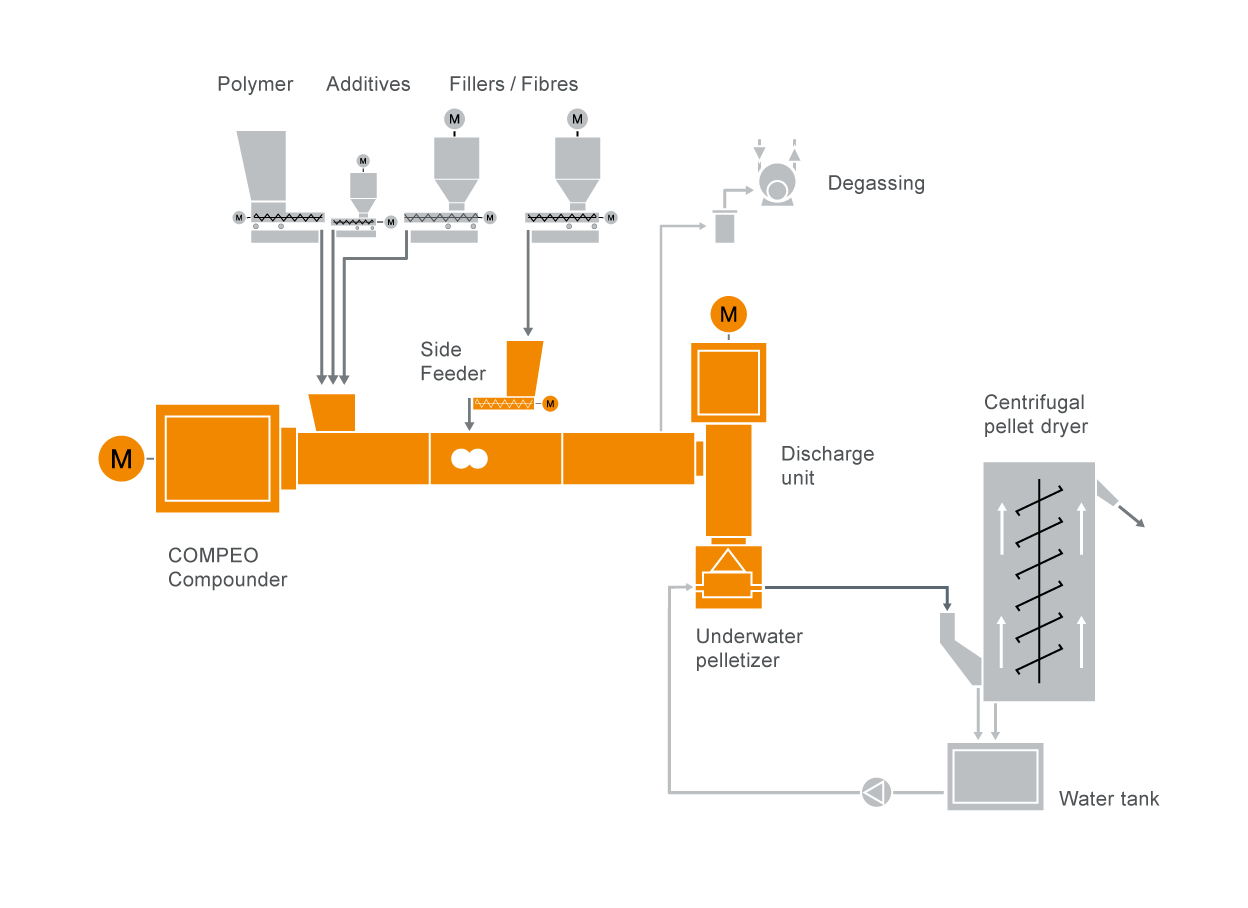
BUSS FRTP compounding systems offer the following specific benefits
Learn More
Downloads
-
COMPEO
-
Laboratory Kneader MX 30