Compounding systems for Soft PVC
The creation of PVC from vinyl chloride (VC) was first described during the first half of the nineteenth century. Large-scale PVC production started in 1928 in the USA and 1930 in Germany. By the time the Second World War ended, it was already the most-produced plastic. With a chlorine content of 56.7% molar mass, PVC is a welcome co-product in chlorine production. Due to their low content of hydrocarbon-based components, PVC materials have a comparatively favourable energy balance and CO2 footprint.
With plasticizers and other additives, the characteristics of PVC materials can be customized according to application requirements.
From the mechanical point of view, these plasticizers can be regarded as “hinges” or “spacers” from the neighbouring macromolecules. The larger the plasticizer molecules, the lower the migration rate under extreme loading.
Soft PVC (PVC-P) in general is produced in the compounding system by hot/cold mixing in the powder phase followed by compounding and pelletizing on a Buss Kneader for all subsequent processes requiring a pellet or granulate. The substantial content of plasticizers, stabilizer packages, and in many cases, high fillers content as well, demand targeted and precisely controlled processing.
Typical applications
The wide application temperature range of -50 to 70°C (sustained) enables various applications such as hoses, plugs and buffer elements. Thanks to its good electrical insulation properties, soft PVC (PVC-P) is the preferred wire and cable insulation material for voltages up to 10 kV. Soft PVC is very widely used in the building industry, e.g. for sealing wall joints and windows, as elastic or sliding coverage material, for surfacing floors, tables and walls, and for many other applications. In medical technology, highly sophisticated systems for conserving blood and infusion solutions are made almost exclusively of this material. There are numerous other applications in the automobile, packaging and clothing industries that have existed for a long time and are being improved and developed continuously. With regard to sustainability and growth, please refer to the section on hard PVC applications.
Compounding requirements for Soft PVC
Compounding requirements can be summed up as follows. The plasticizers and other constituents like stabilizers, additives, fillers, reinforcement materials and flame retardants are absorbed into the porous PVC grain and must be systematically gelled, dispersively and distributively mixed, and agglomerated in the compounding systems – all in compliance with well-defined temperature limits.
Additional property requirements can be achieved by alloying other polymers with PVC during the compounding process. Examples of this include the use of TPU with flexible PVC to improve abrasion resistance, as well as oil and flame resistance. PVC and Nitrile Rubber blends improve low temperature flexibility and chemical resistance. PVC with nitrile rubber or TPU can be alloyed to improve hot melt strength got medical applications, as well as abrasion resistance and durability. PVC/EVA provide reduced plasticizer volatility and improved chemical resistance, while PVC/CPE provides improved compression set and low temperature flexibility.
The Buss Kneader can make the most of its strengths profile at uniform, moderate and if necessary adjustable shear rates. Free capacities along the processing axis are designed and realized according to requirements. Low specific energies with the most intensive mixing processes, volumetric scale-up procedures, and maximum availability are possible due to wide operation windows. These are the advantages that underline more than sixty years of technological and market importance in compounding plasticized PVC.
Typical plant layout for compounding soft PVC
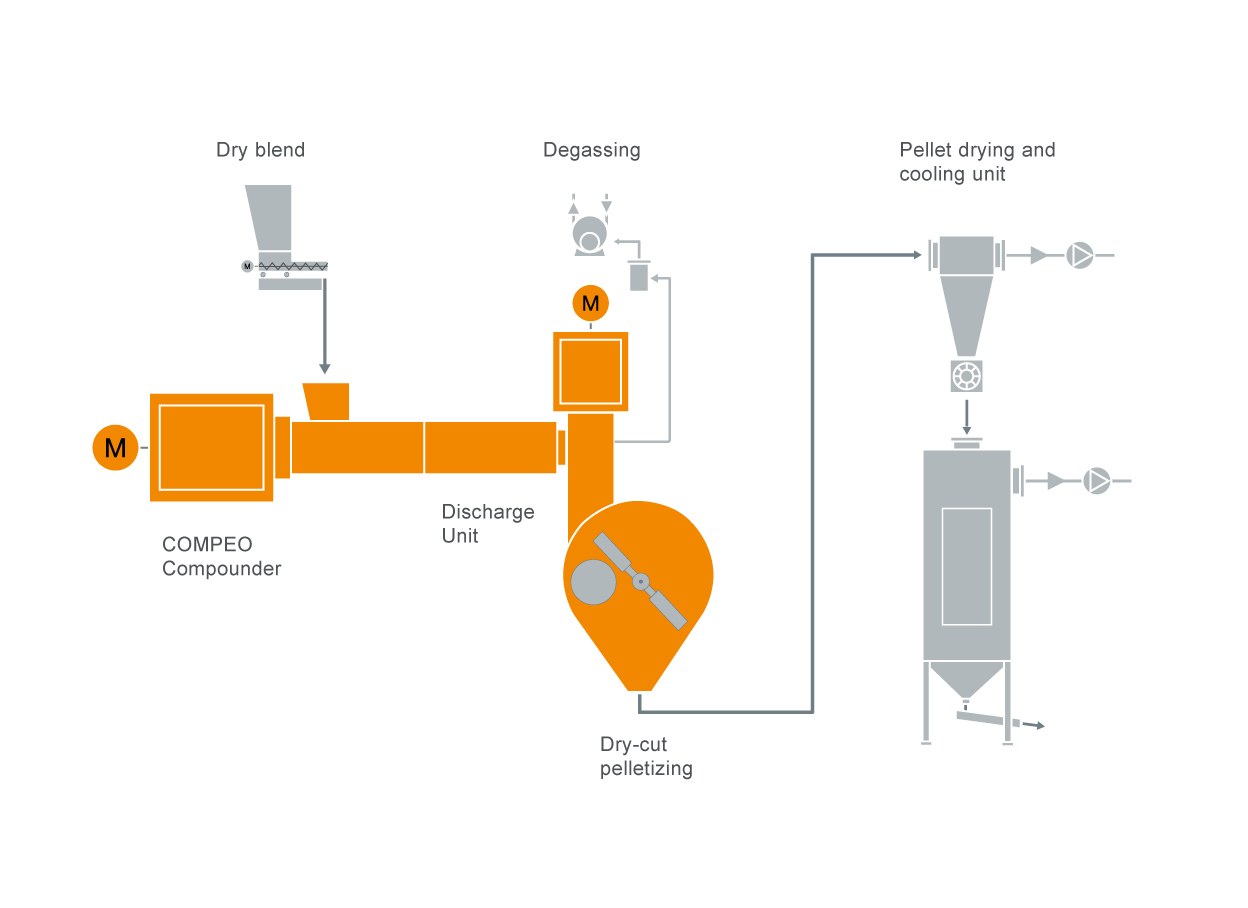
BUSS compounding systems for compounding soft pvc offer the following specific benefits
Learn More
Downloads
-
COMPEO