Compounding technology for Thermosets
Thermosetting plastics, also known as thermosets, are plastics that become rigid and nondeformable after hardening. They are one of the three different groups into which polymers can be divided – thermoplastics, elastomers and thermosets – according to thermosetting degree of the macromolecular chains. While thermoplastics have no cross-linking thermosetting points and are therefore fusible, elastomers and thermosets are thermosetting, not fusible, and disintegrate if the decay temperature is exceeded (pyrolysis).
Bakelite, a phenoplastic, was the first thermoset to be industrially produced at the beginning of the twentieth century. Bakelite was invented by Leo Henricus Baekeland a Belgian-American chemist.
Thermosets are rigid vitreous polymer materials three-dimensionally cross-linked by chemical primary valency bonds. The bonds are created when preliminary products chemically react with molecular chains, either at room temperature with the help of catalysts, or thermally activated at high temperatures. The extremely high thermo-mechanical strength of thermosetsprovide excellent electrical properties and exceptional resistance to chemicals due to their high cross-linking density, but also places high demands on thermoset compounding technology.
Typical applications
These properties define the respective application fields for the compounding technology. High-strength thermosets are used for example in the automobile industry for technical components in engine compartments or drive trains, particularly because of their heat resistance under heavy loading. In electrical systems their combined properties of good insulation, positive fire behaviour and indeformability are paramount. Their good resistance to numerous gaseous and liquid media also makes thermosets first choice for the food and chemical industries.
Compounding requirements for Thermosets
Thermosetting polymer production starts by compounding polymer pre-products with glass or carbon reinforcement fibers, fillers or natural fibers. This is followed in many cases by the respective reaction systems for final thermosetting. Gentle incorporation of the additives is just as essential as strict compliance with the absolute temperature limits required for thermosets. The BUSS conpounding technology and especially the BUSS Kneader handles this perfectly thanks to its harmonic operating principle, with a relaxation phase after each graduated shear stroke. Optimal process temperatures can be verified at all times by precise measurement of the product temperature through hollow-bored kneading bolts fitted with thermocouples at several locations along the processing section. As a result of custom-tailored materials engineering, optimally long service life is typical for thermosetting materials.
BUSS Kneader technology is perfectly suited to the compounding of thermosets due to its cost-effective throughput and the numerous advantages of continuous production. These include unwaveringly excellent and reproducible product quality, renown temperature control, optimal
plant utilization and high production yields. After compounding, the thermosets are rolled out and crushed. Some of these products, such as phenoplastics and melamine resins, can also be hot-pelletized. This brings further productivity gains over alternative processing methods.
Together with broadly based BUSS compounding process expertise, the BUSS Kneader is therefore a good choice for continuous thermoset compounding, as witnessed by the numerous plants already installed in this field throughout the world.
Typical plant layout for compounding Aminoplasts
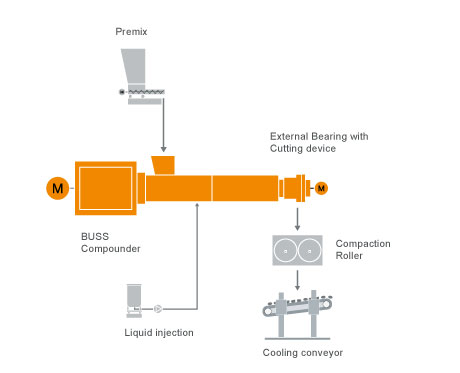
Typical plant layout for compounding Epoxies
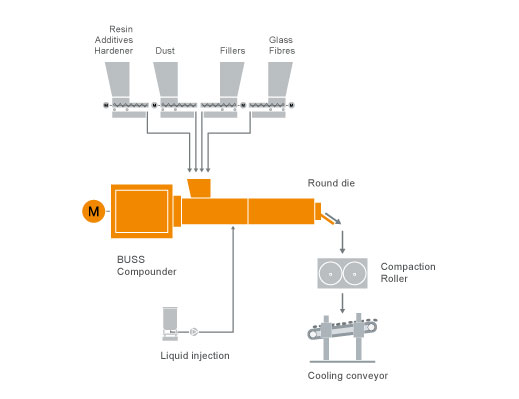
Typical plant layout for compounding Phenolics
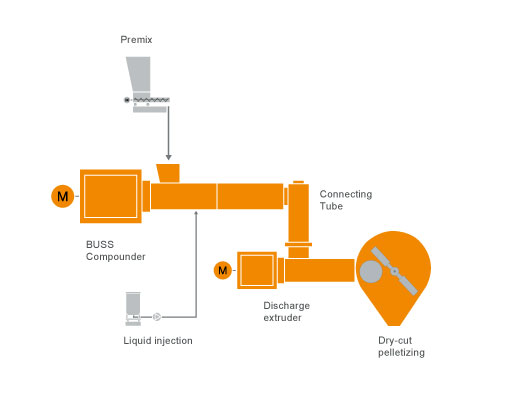
BUSS compounding systems offer the following specific benefits
Learn More
Downloads
-
COMPEO
-
Laboratory Kneader MX 30