The BUSS COMPEO is used in the plastics industry wherever there is demanding processing of extremely high-quality compounds. The new generation compounding system has been designed in a modular way to allow it to be used for a wide range of applications. For PVC compounding, the global market leader in pioneering compounding technology has further optimised the COMPEO. Two years after the introduction of this revolutionary Kneader generation, BUSS presents another configuration of the modular COMPEO range with a cascade design optimised for PVC processing.
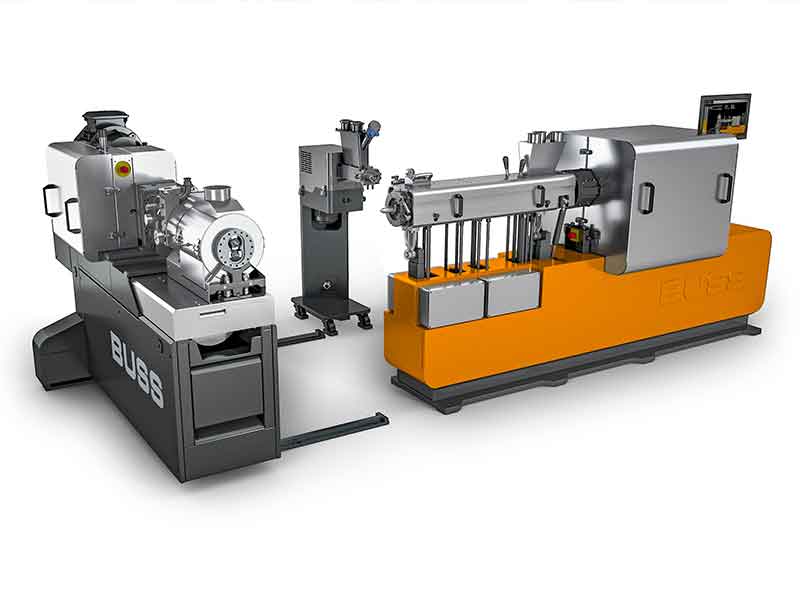
Optimised for processing sensitive PVC
In the two-stage version of the COMPEO in cascade design, the discharge and pelletizing unit is mechanically decoupled from the compounder and is fed in free fall via a connecting tube. The process engineering advantages are obvious. Because the compounding and pelletizing process steps are decoupled, no back pressure is created in the transition area between the compounder and the discharge unit. This offers a decisive advantage when processing sensitive products such as PVC. The melt can be degassed in the connecting tube, which at the same time allows the process section of the compounder to be shortened by the degassing module. This enables a more compact machine, but also reduces the residence time of degradation-critical polymer in the process chamber.
Pivoting connecting tube for easier, space-saving work
In developing this system configuration, BUSS has built on the experience gained with previous models and further optimised ease of use. For example, the pivoting COMPEO connecting tube is equipped with a start-up diverter valve that simplifies and shortens starting up when processing highly filled compounds. This reduces the amount of ungelled start-up material to a minimum. A sight glass allows visual assessment of the compound and – supported by a temperature sensor in the connecting tube – also serves to monitor potential fill-up. Both the tube and the diverter valve can be moved without tools, which allows for easy operation and cleaning. Additionally, the COMPEO in cascade design requires less space than previous models. The fact that the connecting tube can pivot means that there is no need for a retractable discharge unit, which in turn saves space.
Additional flexibility through an alternative discharge unit
The COMPEO in cascade design generates pressure for pelletizing with a single tube discharge unit arranged at a 90-degree angle to the compounder. The discharge screw is equipped with an elongated feed opening, which in combination with the large screw diameter, results in optimum feed characteristics. While the screw tube is water tempered, the screw housing is electrically heated and air-cooled. The discharge screw is designed in 4 or 6 L/D, depending on the pressure build-up requirements. The short 4 L/D version can be extended at any time if necessary. With this alternative discharge option, BUSS underlines the modularity of the COMPEO series. It benefits from the advantages of the discharge units that have proven themselves over decades, particular with regard to PVC processing.
Pelletizing unit with maximum safety and ease of use
The BUSS die-face pelletizing unit is equipped with a two-, three-, or four-bladed knife arm, depending on process requirements. An adjustable knife drive allows the distance between knife and die plate to be optimised during operation. This leads to optimal cutting quality and, in turn, to uniform, cylindrical pellets. This is also served by powerful and homogenous heating of the die plate. A large viewing window enables a perfect view of the die plate and thus optimal monitoring of the process area.
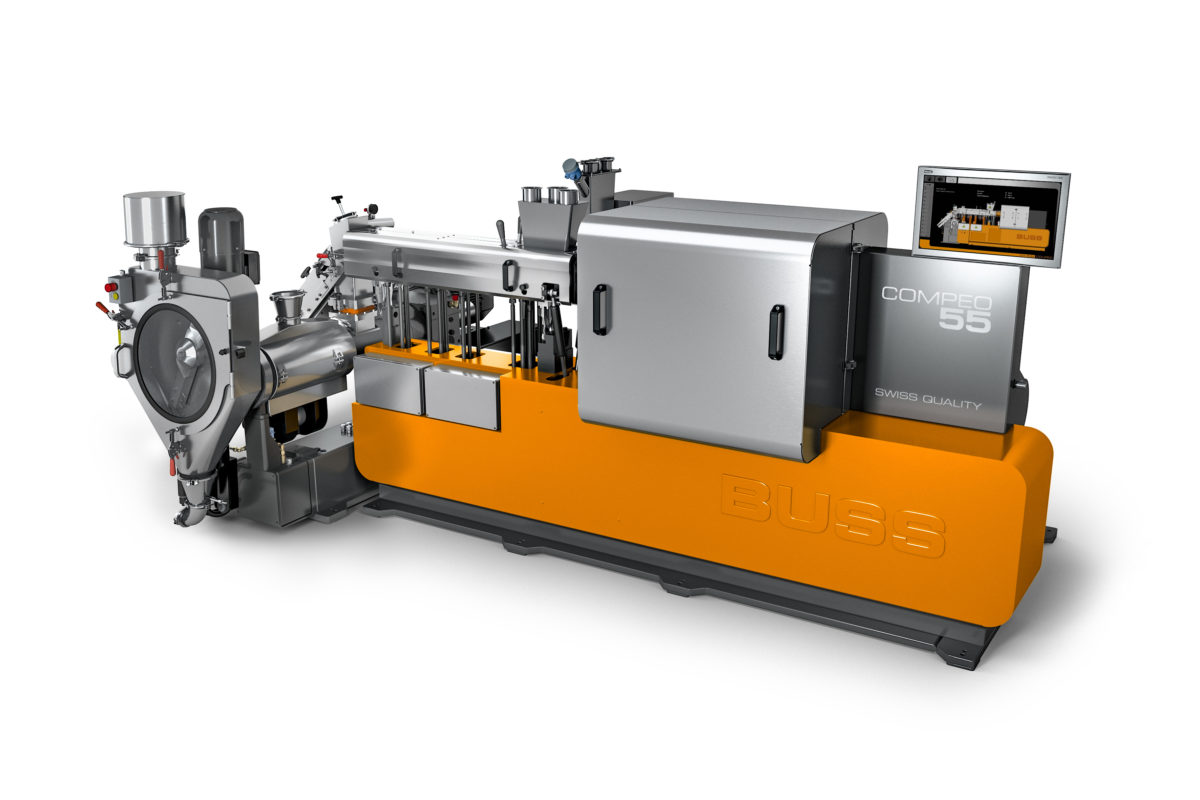
COMPEO 55 including pelletizing unit
The fully swivel-mounted pelletizing unit is installed on the discharge unit to save space and offers the best possible accessibility for cleaning and maintenance. Ease of use and operator safety were top priorities in the development of this pelletizing unit. The die plate, which permits visual monitoring of the pelletizing process, is equipped with a pressure sensor which activates an automatic safety shutdown if the maximum permissible pressure is exceeded. A braked motor ensures that the knife drive is locked securely. The knife arm itself is equipped with a standstill monitor. Access to the pelletizing area is only possible when the system is in a secured state.
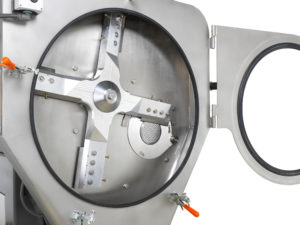
Pelletizing unit with a four-bladed knife arm
This advancement in the modular COMPEO series is based on 70 years of experience in processing technology and machine design. Proven elements are reviewed, developed, and optimised by BUSS to meet current customer requirements and form the building blocks of a versatile and efficient machine concept.
Find out more about the flexibility and versatility of the COMPEO compounding system here: COMPEO Compounding System
Find out about PVC compounding with BUSS compounding technology here: BUSS Compounding Technology